One of the greatest parts of the human experience is that everyone is perfectly imperfect. Yes, even you are imperfect. Besides, a world full of perfect people would be boring, or a Zack Snyder film. Because we’re imperfect, humans can be prone to making downright silly mistakes, and that can translate directly to wrenching. Screwing up while wrenching can cost you time, money, or even your safety. So, what was your dumbest mistake while wrenching? How much pain have you caused yourself fixing a car?
Admittedly, I have a bunch of stories of screwing up with cars. There was the time when the return line nipple on the gas tank of my doorless Ford Festiva broke during an off-road rally. I didn’t know that I could have just blocked off the return line, and instead, I attempted a wild trail repair. I crafted a new return line nipple out of duct tape, 50cc scooter fuel hose, and J-B Weld. It looked gnarly and was probably all kinds of unsafe, but it stopped the leak, at least long enough for the car to die in an off-road park.


Take a look at my awful work:
It was a dumb mistake to attempt a repair like that on such a critical part of a vehicle, and it’s arguably not the dumbest thing I’ve done while wrenching.
In 2020, I traded a $500 Mercedes-Benz 240D sedan with a blown differential for a second-generation Ford Ranger with a crushed left radius arm. I’m smart enough to know when a job is beyond my skill or tools, and I farmed out the radius arm replacement to a shop. I did the trade for the truck because Sheryl and I needed a vehicle to drive across the country to participate in the original Gambler 500 run in Oregon.
This vehicle needed to drive about 5,000 miles all in one trip, so I did the right thing and replaced anything goofy.
My inspection revealed that after the radius arm was replaced, the Ranger needed new power steering lines, new front brakes, and new front bearings. That’s not a lot of work and I knocked it out in a weekend. The power steering lines put up a fight, but cutting them off with a steak knife made replacing them easier.
Bearings on an old truck like this are also super easy, barely an inconvenience. I did them while fitting new rotors and pads up front a few nights before leaving for the Gambler 500. I capped off what I thought was a job well done with sweet American Racing wheels with all-terrain tires. My sweet technically $500 Ford Ranger was ready to rock.
On my first test drive the night before our departure, I realized my first dumb mistake. See, this Ranger had the economical, yet gutless four-cylinder engine. It simply didn’t have the power to propel the truck faster than 60 mph with those big tires, and that was with the throttle pinned. But I had exactly no time to find replacement tires. I had to run the truck’s original tiny tires in the rear with some spare larger wheels up front.
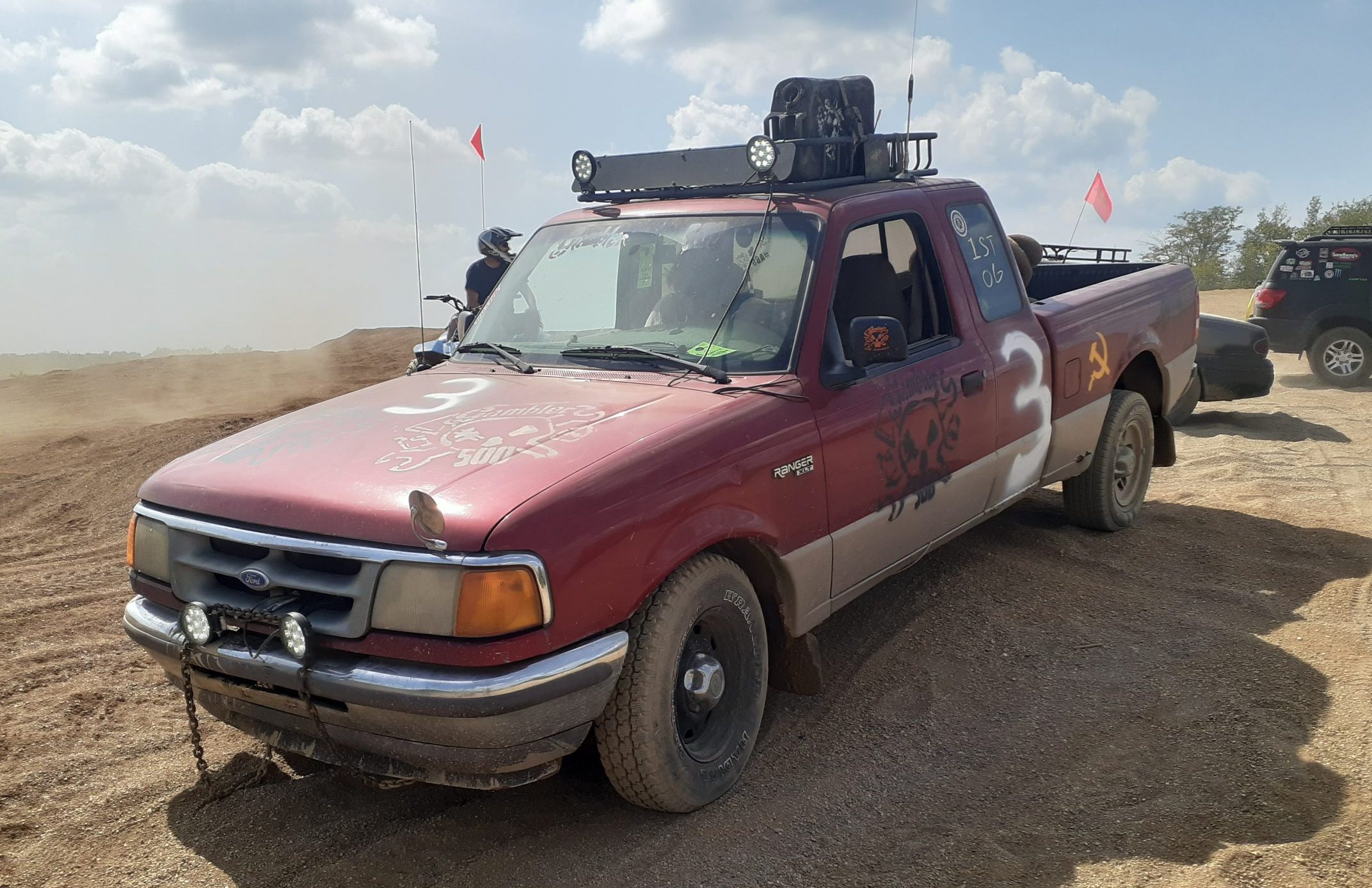
On the first day of our Gambler trip and about 200 miles in, I started hearing a weird scraping noise every time I applied the brakes. After about 250 miles, I decided to tell my friends, one of whom is a diesel mechanic, and we started looking over the truck. The problem was apparent the moment the front wheels were removed. One bolt securing the left brake caliper was missing while the other bolt was not even finger-tight. The slide bolt was also missing. The only thing that held the caliper in was the inside of the wheel and the fresh brake pads.
I could have sworn that I tightened those bolts, but I was also a few White Claws deep that night, so maybe I skipped that step and just put the wheels on. What I do know is that after we sourced the missing bolts and tightened everything down, it never happened again. I no longer drink while wrenching.
Have you done anything dumber? What was your silliest mistake while wrenching?
I learned that you shouldn’t keep gasoline in unmarked containers. My dad put a big red Folgers coffee can of what he thought was gasoline inside the tank of my 1981 Honda CB900C. It was in fact industrial strength undiluted vinyl siding cleaner. This melted all the rubber inside all 4 carbs, basically bricking the bike. After that I got to learn all about rebuilding and synching 4 motorcycle carbs.
My dad and your dad woulda been good friends.
Corollary: Do NOT bleed brakes into an empty bottle of what you are currently drinking (eg: Mt Dew).
For the record, The Poison Control Center surprisingly says that used brake fluid is not considered highly toxic—but (at least 10 years ago) were unsure whether one should induce vomiting if actually ingested. I didn’t swallow—but have always since used a clear container with some sort of colored tape around it. I try to learn from my mistakes 😉
My dad always used old pickle jars , I power bleed myself.
Separately, I learned not to use glass containers.
Seems I’m always learning >something<
This is so easy.
Never, ever use a 6-point Torx bit on a Triple-square fastener.
I did this while doing the front wheel hubs on my MkV Golf. Stripped them all! And then went through about 400 drill bits hogging those fuckers out.
Several days of arm-vibrating torture that could’ve been spared by going to Harbor Freight and buying a $15 tool.
Hmm so many of them, safety wise don’t wear your metal watch strap near the battery, working- compare the old and new parts then throw out the old so you don’t reinstall it. And the biggest one, dont’ assume that the shop who did the work on the car previously did it correctly
Oh, I know a good one. Don’t wear short pants on a really hot and humid day working on the electrical system of a car. If you find, somehow that you are doing exactly that for God’s sake, don’t put your sweaty kneecaps against the chrome bumper while you’re installing the battery.
Reminds me of one of mine. When bent over for a long time working on a car on a sunny day, sunblock the place where your shorts and shirt are supposed to meet. That is one annoyingly uncomfortable place to get a sunburn.
Or even wear a watch while you’re working; I stopped doing that years back after ruining the strap on a beloved timepiece.
yeah mine got red hot and left a scar around my wrist- the worst was the smell of cooking pork- lucky it wasn’t a sentimental watch, I lost the Seiko my dad bought in Hong Kong in 69 somehow
Yikes – that’s a helluva wrenching souvenir.
I also no longer wear a watch while riding motorcycles off road, after I managed to destroy one during an otherwise uneventful crash. It was just an old Timex, but I’m a huge fan of them so it made me sad to lose it.
I learned this the hard way multiple times. I’ve wrecked the faces of so many watches over the years shoving my hand into tight spaces with sharp metal bits around. It’s actually the reason I have a wall clock in my barn, just so I have no reason to leave my watch on when I’m working on something.
Recently, I developed a water leak on my MK6 GTI which I thought was the water pump (it was not) which almost turned into an ordeal.
One night I got home and found coolant dripping on the ground. Did a pressure check, which held, and saw nothing obvious but after a few days I could see coolant seeping from the water pump. Typical VW problem for this era so I bought a water pump and related parts to get the job done.
I am a big “while I am in there” kind of person and decided to swap out the seal on the balance shaft that runs the water pump. There is a left handed thread bolt that holds everything in place which I was able to get out relatively easy and popped out the seal which was also pretty easy. The FSM recommended a special seal installation tool, which I bought, and I set out to install the seal. The left handed thread bolt is known to snap if you look it at funny so I bought two new bolts of which one was just to install the seal with the special tool. You tighten the left handed thread bolt and the tool pushes the seal until it reaches where it needs to be.
Well, being a goober, I over tightened the bolt and it snapped off. Anyone who has ever snapped a bolt knows the dread that you just screwed up. After walking up and down the driveway swearing at myself and feeling like I was going to throw up I steady myself and began to research how to get this broken bolt out.
Now typically, I use a left handed drill bit and drill until the screw comes out but no dice this time. There was only a 1.25 inch gap to insert a drill and a right angle adapter was to wide. I spent some time online and saw someone had gotten it out by JB welding a bolt to the broken piece but I had no luck.
Resigned to the fact that I needed to remove the balance shaft, from the front side of the engine, I began reading the FSM and discovered that it was essentially a timing chain job (which I had paid $2k for a shop to do the previous year). No effing way I was going to do that job or pay someone else to do it. Oh, and the balance shaft? One time use. Once you remove it, the FSM states you have to replace it. Balance shafts are only available from VW and they are sold in pairs ($800). I did not have the time to do it (work and family) and my pride stopped me from taking it to a shop to fix it. So the car sat for six months in my garage.
When time permitted I looked for alternatives and began to look at the problem from a different perspective. I needed the right tool for the job at hand. A few hours of online research later I found an aerospace tool company that made just what I needed. A slim right angle offset drill adapter that could get into this 1.25 inch gap. I ordered the adapter and different size drill bits ($200) and waited for the new tools to arrive.
The big day came and I hooked up the adapter to my power drill. I could not see the center of the broken bolt so closed my eyes and went full send. 15 seconds later the broken bolt came out and the relief nearly overwhelmed me. “I did a thing!” as Jeremy Clarkson would say.
With that disaster averted, I finished the water pump replacement and bolted everything back into its place proud of myself for fixing the problem that I had created. Took the car for a drive and the car leaked coolant from the same…damn…spot.
Turns out one of coolant hoses had fatigued and would sporadically lose its ability to maintain its seal on the water pump. All that work and it was a simple coolant hose that needed to be replaced.
If that happened to me, I’d end up on the news.
It was an exquisite climax before the denouement, anyway. What relief it must have been to get the bolt!
Don’t start the engine to find a lost tool. While fun to hear the “zing” as it goes flying, the “thwack” as it hits something is not as fun.
oooh the 10mm was inside the intake, upstream of the turbo, my bad
The lessons I learned:
1) Be patient, as much as humanly possible. Being impatient leads to errors, errors lead to more impatience, then to anger. Anger leads to the dark side.
This also includes spraying penetrant on rusty bolts and nuts, whacking then a couple of times with a hammer, and walking away for a while. Then repeat. Leave it overnight if you can. When you come back, that bolt will probably come off. Patience pays.
2) I have two notches on my strength continuum: not quite enough and way the hell too much. The latter is especially a problem for lesson 1, above.
3) Don’t be stubborn — ask for help if you need it. I went at the back upper O2 sensor on my CSVT for an hour, hacking up my forearm in the process. I am a big guy, so my hand was hard to fit in the space. Then I saw my neighbour who was a Class A mechanic and Vietnamese. “Hey, could you come here for a minute please…?” 20 seconds later, the sensor was out.
4) Have your shit together. Nothing slows down a job like having to bum a ride to the parts/tools store three times. Nothing.
Re: #1. I spray penetrant oil, tap it, talk to it, tap harder on it—then use a small ratchet and slightly >tighten< the fastener before putting pressure on the end of the ratchet and tapping on the middle-end with an extension. This is my approximation of a low-torque impact. Have yet to break a small bolt since adopting this technique.
I really believe in the multiple spray & tapping technique. Also, as you say, patience is key. If rushed or angry, I abort.
Don’t rush, take your time, ask for help, know how long procedures take.
If it feels unsafe, stop, walk away, re-assess, come back later with help.
I’ve made a couple of recent, very expensive mistakes because I’ve been in an unnecessary hurry….
1) removing the multimedia unit from my Touareg to hook up an aftermarket android auto/apple car play unit requires a couple of flat metal keys to unlock and slide out the unit. I didn’t have these keys on hand and totally didn’t need to finish this job right away but I DID have a couple of small jigsaw blades that sorta fit. They were also way too long, dug way too deep in the keyholes, and shorted something in the head unit letting out the smoke. A used replacement shipped from Europe was $600 + a couple hundred bucks at the dealer for reprogramming, all because I was in a hurry. DUMB.
2) this one stings the most. I really, really wanted to mount the hood on my Porsche 944 turbo project. It had been going for 6 years and this was one of the last things to do before it was ‘done.’ The hood is big and it’s heavy. I got it about in place with two bolts holding it in, but it was slightly out of alignment. Without a helper to hold it up or check it closing with me, I went to lightly shut the hood to get the rest of the bolts when I heard a ‘crrrrrrrrrrack’ from the back of the hood. The corner of the hood clipped the brand new windshield on its way down and sent a nice crack halfway through it. SO, SO, DUMB.
Always make sure the old oil filter gasket has come off with the old filter before attempting to tighten down the new filter.
Double points if you remember to do this on a engine containing 11 quarts of oil.
Always inspect the work of the person you are teaching. Girlfriend (now wife) wanted to be ‘more involved’ with her car (MGB), so we started with oil changes. The cross-threaded the filter and I didn’t check it. “Is there supposed to be that much oil everywhere?”
Speaking of fluids: if you’re replacing any kind of fluid and your funnel doesn’t fit, or the fluid you’re putting in takes forever to go down, stop and double check you’re putting the right fluid into the right pipes.
I make a point to wipe down the mating surface on the engine, in part because it makes it very hard to miss a stuck gasket.
That is now my practice as well, and for the same reason.
If it crosses your mind that it may be a good idea to unhook the battery before doing the job, then you need to unhook it. If it doesn’t cross your mind, still a decent chance you need to unhook it.
Thanks to a previous piece here, I’ve also become a lot more aware of what part of me could touch what what part of the car if I’m working near the battery/something electrical and something slips.
I specifically picked out a wedding ring made of a non-conductive material after seeing the results of someone bridging a connection with their wedding ring. They stated it glowed red from the heat and had to be cut off their finger. A lot of times I still just put on a silicone one to be extra sure.
Always disconnect power. Turn off breakers at the panel for your house, unplug power tools (don’t just rely on the switch) when you’re not actively using them, and disconnect any batteries. Always, no exceptions. None, ever.
When looking for a current draw from the battery when the car’s off… always remember to close the doors. Spent hours chasing a draw that ended up being the dome light from the door not being completely shut
This is even tougher on cars with the battery in the trunk AND a trunk light.
Never assume replacement parts are identical to the originals.
Back when I had my 1991 Miata, I did a bunch of suspension work, including new tie rod ends. I marked the tie rods before unthreading the old ends, and counted the number of turns it took to take them off, figuring I could thread the new ones on the same number of turns and at least be in the ballpark, then take the car to get an alignment after I was done with everything else.
What I didn’t notice was that the threaded portion of my shiny new tie rod ends were about 1/4″ longer than the originals. I dutifully screwed them on the same number of turns, buttoned everything up, and went to take the car for a little test drive.
With about three degrees of toe-out on each front wheel.
I only made it as far as the end of my block before I knew something was very wrong. It wouldn’t go in a straight line, turn-in was downright scary, and it felt like it was going to lunge into one curb or another even at 20 mph. Absolutely terrifying. After comparing the old tie rods to the new (which I should have done in the first place), I saw the problem, measured the difference between old and new, and screwed the new ones on by that much more, and everything was fine again.
Ever since then, I always hold a new part up to the old part, before even disassembling anything if I can, just to make sure. Because even if something “fits,” that doesn’t mean it’s exactly the same.
A related corollary is to compare the parts before you remove the old part from the car if possible. That way you aren’t stranded with a disassembled vehicle and the wrong part
It also allows you to find the hidden fastener
Speaking of hidden fasteners, what I wish I’d known or thought about is that old trim clips are metal, fatigued, sharp, and everywhere. This means they’re probably rusty, they will break as you try to remove them or deform such that they won’t snap back snugly when you reuse them, they WILL make you bleed, there will ALWAYS be another clip to remove that door card or speaker grille, you will never have enough replacements on hand, and because they’re such a bitch to deal with, you’ll say fuck it and forgo two clips because you didn’t buy enough, put the trim back on, and regret it for the rest of your life because everything is rattling but you can’t be added to pull the trim back out and do the job again.
Fuck clips
And then there are the ones using slightly different clips to confuse you
Make sure you can get the parts you need before you take everything apart. Or be prepared not to.
Broke a bolt swapping out a wheel bearing assembly. Oh look it’s 9pm. Hunny, you don’t need to drive to work tomorrow do you? Then finding out you can’t buy that bolt anymore and searching a hardware store for the next best thing while the car sits on stands, halfway in the garage (so it can’t close) for 2 days until I can find what I need.
Also, always check to make sure the rubber gasket is actually on the oil filter before you leave the store.
Nice…so I’m not the only one that opens the box and inspects the filter before I pay for it!
ALWAYS put blocks behind your tires when the other 2 are on ramps. You’d be surprised how far a MGB can roll on 3 tires 🙁
And don’t assume that the parking brake on the car you just worked on is working when you kick those blocks out- a 2.8 Capri is too heavy to stop with your leg
I learned about shaft phasing the hard way.
I had to replace the gearbox on a Kubota mower deck on a big diesel zero-turn. When I was putting things back together the drive shaft didn’t want to slide onto the splines of the gearbox yoke. A smack with a hammer and everything went together just fine. Turns out that the only thing preventing you from putting the shaft together with the two u-joints on each end of the shaft being out of phase was a tiny little weld bead between splines. Which pops right off with a smack from a hammer.
The vibration was horrible, but I believed the gearbox assembly or adjustment was bad, for reasons, and ran it anyway.
Destroyed the PTO clutch system and bearings internal to the zero-turn’s transmission. This is when I learned about shaft phasing. A $4000 education that I can’t for the life of me understand why I didn’t figure out much sooner. Like decades sooner.
Photos, lots of photos before and during disassembly.
Using the shitty oem jack on a questionable surface. Too small contact area, should have known better… Could have ended real bad without the tyre as a backup ”stand”.
Pay attention. Don’t rush.
Toyota needs an oil change. Wife needs car in 20 minutes. I can do that!
Put car on ramps. Throw pan under car, remove drain plug… After about a quart drains… That’s not the right color?! Put plug back as fast!
Honey, car won’t be ready. How about I drive you?
My Mazda has a 8mm internal-hex/Allen head for the oil pan. The Toyota has an 8mm internal-hex/Allen head for the transmission, and an external hex for oil. In my rush I drained the ATF.
After buying a gallon of very very expensive CVT-ATF from the dealer, I topped up the trans, then completed the oil change.
Most expensive oil change ever!
I drained the oil, replaced the filter, and proceeded to fill a recently rebuilt transmission with motor oil.
That was also an expensive oil change, considering that engine likes expensive dino oil and its 8 big cylinders are thirsty.
Bearings and hammers don’t mix during the installation stage.
Don’t “that’ll do her” when installing spark plugs. Find out the proper torque setting. If you don’t, the plugs can start working themselves out and will cause all kinds of trouble.
I don’t believe in using torque specs for spark plugs. As they get carbon and stuff in them it isn’t accurate any more. I do it the same as an oil drain plug, handtight then half a turn. With a 3/8 ratchet you can feel if this is snug or not by turning it gripping just the area around the head of the ratchet with your palm.
Somewhere I heard or learned that placing your palm on the ratchet head and snugging with just 3rd finger & pinky was ~11 ft-lbs—that’s what the acorn nuts for the old air-cooled VW oil-strainer cover were supposed to get. Must be fairly close as I never stripped one
—now I’m wondering if that was in Muir’s Idiot’s Manual. That was a Bible to me early on
11 ft-lbs is actually my target spec usually. That’s the “magic number” for Ford heads with the dreaded 4 spark plug threads which is supposed to prevent them stripping or blowing out. So it is funny that that’s the number they say is produced with this method since that’s what all the Ford techs say they do.
Always use a torque wrench set to the proper spec for whatever you’re doing.
That will help you to avoid the snapping sound the bolt makes after one too many ugga-duggas. 😐
Also learn how to use an extractor before you need to use an extractor.
Nothing like the sinking feeling you get when you’re torqueing a bolt to “gutentight” and it starts getting looser…
It’s like having your life flash before your eyes, only it’s the future… All the trouble ahead of you, hours potentially, just to fix the last 2 seconds…
Especially with torque to yield hardware. My current cars are full of aluminum, one time use fasteners that get torques like 5nm+90 degrees. Don’t reuse one-time-use hardware, and use a torque wrench when you install it. Mark the head or use an angle gauge for final turns. Last year my battery stopped charging. Come to find out it threw the belt off the alternator, and the reason that happened is someone re-used the hardware that holds the A/C compressor to the block, so it was literally hanging on by a thread on one bolt, and the other 3 bolts had broken off in the block. All to save $15 in hardware.
I ditto everything said! I also hate torque to yeild hardware. I get it, but hate it.
@Jb996, well said. “…flash before your eyes….” I’ve done this a few times in my life, for sure. I can remember the first…
…The spark plug on the head of our Cub Cadet 7hp tractor. My dad had to replace it. It was my first “oh fuuuuu” moment. I can still picture it clearly (I have real shit memory too). I don’t recall him being overly angry at me, as I was maybe 12, and didn’t know what torque was yet in my wrenching career. At this point in my experienced engineering life, though, I would helicoil it and put a larger plug in it (probably, cause the heads are probably hard to come by these days).
Yeah had a head bolt do that- I hadn’t cleaned the oil out and it actually snapped during the 180 degree part, stretch bolts too so a new set had to be ordered
Just buy/borrow the right tool for the job. Me trying to be a cheapskate has wasted more time and caused more frustration than buying the right tool. Case in point: using adjustable pliers for spring tension hose clamps. The small ones are no sweat. The big ones on radiator hoses are a pain. Getting a locking hose clamp pliers made removing those child’s play. Or, buying the GM shock tool for replacing shocks on my car. It made an otherwise impossible job doable.
Tl;dr: messing around with bodges when the proper fix is easy with the right tool.
The diagnostic flow chart in the FSM is your friend. Follow that before you jump in to a YouTube video. Spent a couple hours trying to track down an ABS issue before looking at the FSM. Would have saved a bunch of time.
Wayyyyy back in the day, my first car, a 91 Cavalier Z24 5 speed. It kept destroying CV boots and I couldn’t figure out why. I replaced the OE one, drove it around the block and before I got home the boot was already off again. Figured it was a fluke. Took it back to Advance Auto and got a replacement, and of course the same exact thing happened. Of course, with the car jacked and the wheel off, I could see no reason for the boots to rip apart, everything looked fine. Throw another axle it in. Same thing!. Finally I got the bright idea to look around with the suspension loaded, and sure enough with the wheel on and the car on the ground, the axle was hitting the chassis due to a busticated transmission mount.
Similar issue on my current car, but due to my “experience” back when I was 16, I troubleshot it a lot faster this time. My current car was making a groaning sound while braking over bumps at low speeds. Put it up on the quickjacks, take the wheels off….nothing wrong. Immediately I remembered the Cavalier, put it back together and drove it up on ramps, and with the suspension loaded I could see the rubber isolator of the stainless brake lines I installed were rubbing on the axle, and it was exacerbated when braking.
If you’re troubleshooting a noise, vibration, or other gremlin, don’t forget to take a look around with the suspension loaded!
I learned the hard way to read. the. instructions… then read them again. I was swapping suspension on my Miata, a relatively easy job, but went aftermarket for the components, and not pre-assembled coil overs, so I had to slap everything together myself. I forgot the washers on the rear top hats. Assembled everything and as I let the car down I just watched in horror as the shock push rod just rose straight up out of the top hat.
I had to completely remove the assemblies, take them apart, add a single washer to each, and reinstall the assemblies all over again. Not difficult, but that’s a couple hours of my life I will never get back from two little washers I skimmed over when reading the assembly instructions
Don’t secure your air cleaner with tiny nuts that can fall into the carburetor.